Rust on floorboard
#31
Seasoned Member

Fiberglass and Bondo are great for hiding rust behind a nice, thick armor plate, so that rust can do its work unseen and uninterrupted. Only when it has total victory in sight will it poke out from behind its shield where you can see it and counterattack, but by then its usually too late.
That's why I hate powder coating, too. I'd rather see it when it starts, than find out long after structural damage has been done. Paint will let it out where you can see it.
Powder-coating / Bondo / fiberglass all are allies of rust.
That's why I hate powder coating, too. I'd rather see it when it starts, than find out long after structural damage has been done. Paint will let it out where you can see it.
Powder-coating / Bondo / fiberglass all are allies of rust.
If you apply any of the coatings over rust they will enhance the propagation because they trap the entrained moisture that's causing the electrolytic action. You have to remove the rust completely, get down to the base metal and then scarify it to give it the tooth the coatings need to grab into the metal and form a moisture-free bond. Just before applying fiberglass I heat the prepared repair area with a heat-shrink gun to ensure it's moisture free. Then I lay up the initial glass pre-preg and wait for the cure before applying additional laminations. With moisture removed from the repair area, there's no chance of corrosion to begin galvanic action.
Metal must be exposed to moisture and contamination to have the properties necessary for corrosion to start. If one were to believe that coatings were friends of rust, paint (coating) would not deter galvanic events and the metal would corrode beneath it. The only time that occurs is when a bare metal area (chip in paint) begins to rust and the rust creeps under the adjacent paint radially outward in a spiderweb fashion.
The only thing I will never use is Bondo. That stuff is hygroscopic, meaning it absorbs the moisture from the relative humidity in the surrounding air as it cures. Once cured, that moisture is entrained and remains there with no place to go, being sealed in by the paint topcoat, and ultimately begin corroding the metal surface it's bonded to. Once the bond has been completely compromised the Bondo repair will be held in place by the paint topcoat only and appear as a discontinuity in the surface (bump), because the corrosion beneath it has grown and expanded it away from the metal surface.
Rust must be completely removed before any repair can be expected to be durable, and that includes welding.
#32
CF Veteran
Join Date: May 2012
Location: Lost in the wilds of Virginia
Posts: 7,964
Received 956 Likes
on
771 Posts
Year: 1998 Classic (I'll get it running soon....) and 02 Grand
Model: Cherokee (XJ)
Engine: 4.0

I'd rather clean up and repaint a rusted surface than replace structurally unsound parts that got that way because rust was allowed to progress unnoticed.
#33
CF Veteran

you both have good points.
yes the metal has to be absolutely clean of rust and moisture, for either fiberglass or bondo to work. yes bondo is very hygroscopic, but used in the right application (dents, not rust repair) can be very effective.
i agree with the powdercoat argument, it works great at first, till you get a chip in the coating, then rust forms underneath, doing it's dirty work before you get a chance to see it. and if you do, and decide to fix it, it is very difficult to grind that shiite off. i prefer coating my newly fabbed parts with simple tremclad (or rustoleum, for my friends south of the border). easy to spot rust corrosion, and easy to grind/repaint the effected area.
it's all in the prep. if you don't get all the rust, it will show up sooner than later. rust never sleeps.
yes the metal has to be absolutely clean of rust and moisture, for either fiberglass or bondo to work. yes bondo is very hygroscopic, but used in the right application (dents, not rust repair) can be very effective.
i agree with the powdercoat argument, it works great at first, till you get a chip in the coating, then rust forms underneath, doing it's dirty work before you get a chance to see it. and if you do, and decide to fix it, it is very difficult to grind that shiite off. i prefer coating my newly fabbed parts with simple tremclad (or rustoleum, for my friends south of the border). easy to spot rust corrosion, and easy to grind/repaint the effected area.
it's all in the prep. if you don't get all the rust, it will show up sooner than later. rust never sleeps.
#37
CF Veteran
Join Date: May 2012
Location: Lost in the wilds of Virginia
Posts: 7,964
Received 956 Likes
on
771 Posts
Year: 1998 Classic (I'll get it running soon....) and 02 Grand
Model: Cherokee (XJ)
Engine: 4.0

And it's never lonely.
The following users liked this post:
caged (10-22-2019)
#38
CF Veteran
Join Date: Dec 2017
Posts: 4,029
Received 1,117 Likes
on
896 Posts
Year: 1989
Model: Comanche (MJ)
Engine: 4.0

My first thought is that you need a nice autodarkening helmet so you can see where you're welding, and a little practice on some scrap sheet metal to get the voltage/feedrate dialed it a bit better..
#39
Seasoned Member
Thread Starter

I have a quality helmet and when practicing I did a bit better. It was just the awkward positioning and not really being able to clamp the patch down (and me not having a clue how to weld) that led to the welds being what they are. I was also trying to prevent blowing a hole through the pan. I have my lincoln 140 set all the way down with a very slow feed rate, when I turned up the speed alittle it seemed to help. Also I am using flux core for now. But hopefully it holds until I weld in a whole new pan next year, better then nothing.
#40
Senior Member
Join Date: Nov 2016
Location: Homer Georgia
Posts: 703
Received 98 Likes
on
89 Posts
Year: 2000
Model: Cherokee
Engine: 4.0l

I have a quality helmet and when practicing I did a bit better. It was just the awkward positioning and not really being able to clamp the patch down (and me not having a clue how to weld) that led to the welds being what they are. I was also trying to prevent blowing a hole through the pan. I have my lincoln 140 set all the way down with a very slow feed rate, when I turned up the speed alittle it seemed to help. Also I am using flux core for now. But hopefully it holds until I weld in a whole new pan next year, better then nothing.
#44
Seasoned Member
Thread Starter

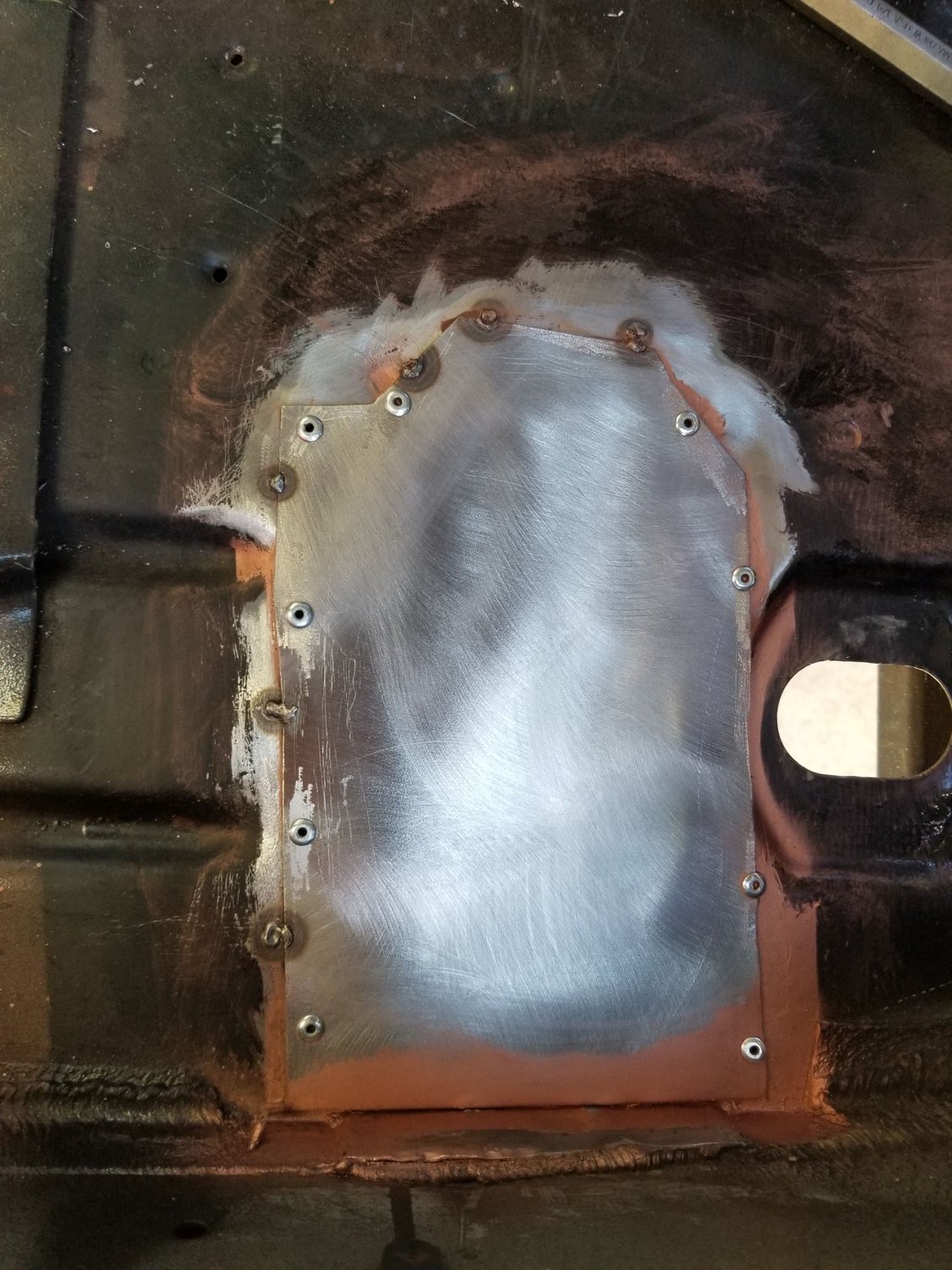
Well on this section I decided to use steel rivets bc of my crappy welds on the first section, then spot weld inbetween. In my opinion my spot welds were much better then the first attempt, that's the good news. Bad news is my lincoln 140 that I have only used a hand full of times will not feed wire, and I didnt get as my welds as I wanted. I'm going to have to find a repair shop to take a look at it.
Last edited by BlackXJay; 11-06-2019 at 02:11 PM.
#45
CF Veteran

check to make sure your wing nut holding your wire spool isn't too tight. or that your drive wheel has the correct amount of tension.