From the Ground Up
#1
Thread Starter
Senior Member
Joined: Oct 2010
Posts: 562
Likes: 0
From: Pagosa Springs, Colorado
Year: 88-ish
Model: Cherokee
Engine: 4.0 I6

So this fab section is for build from the ground up. Being that i can see the Ground through my floor I better try and cover that Up.
This is my new floor im putting in and I'm also going to be replacing the plasitic molding on the sides with some sheet metal storage since I have everything apart anyway. here is the start of my floor. Also this is the first time I have ever welded anything so these welds are not pretty at all. You can make fun if you want but they are holding so im happy with that.
Right after I pulled up the carpet. Way worse then I thought
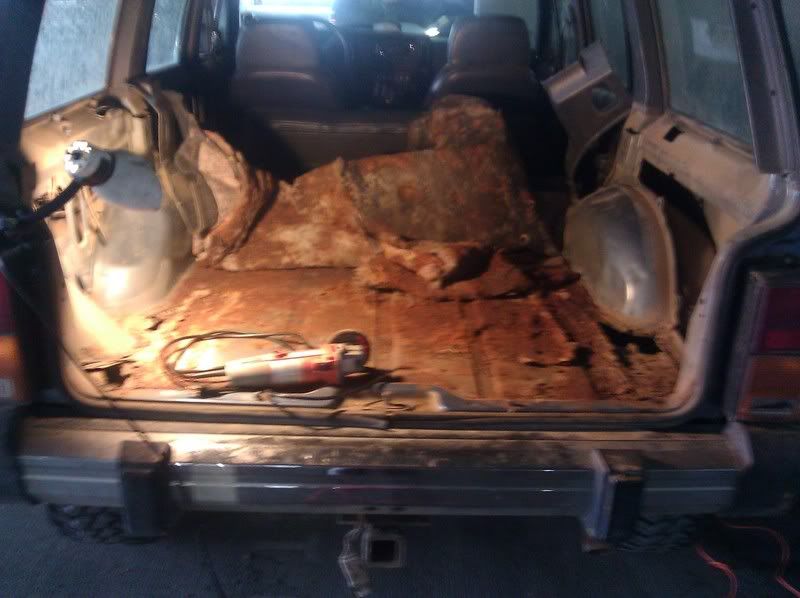
Getting some of it cut out.
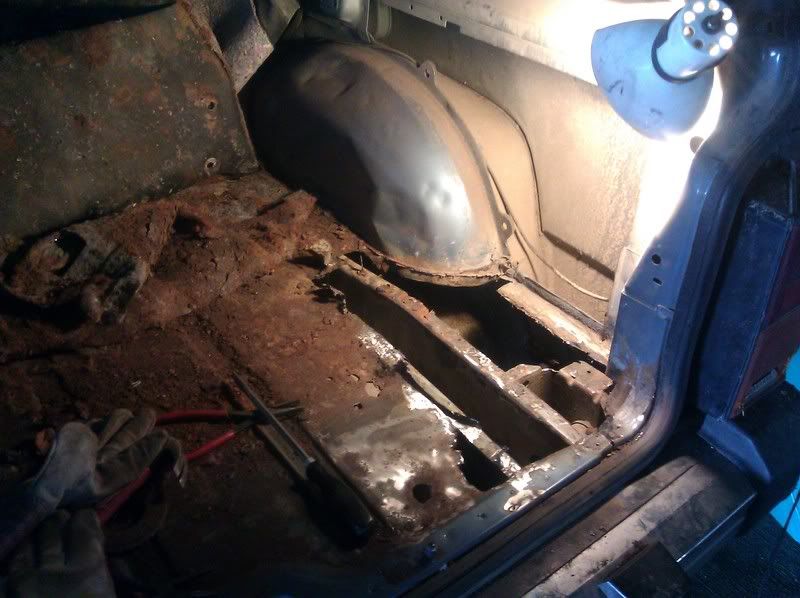
First couple pieces went pretty slow. Now that the corner is almost done I should be able to make fast progress.
This is my new floor im putting in and I'm also going to be replacing the plasitic molding on the sides with some sheet metal storage since I have everything apart anyway. here is the start of my floor. Also this is the first time I have ever welded anything so these welds are not pretty at all. You can make fun if you want but they are holding so im happy with that.
Right after I pulled up the carpet. Way worse then I thought
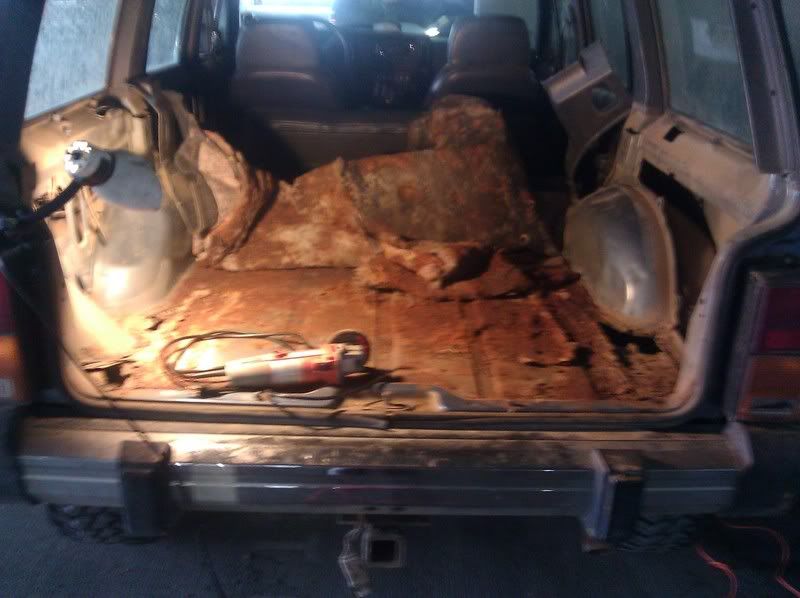
Getting some of it cut out.
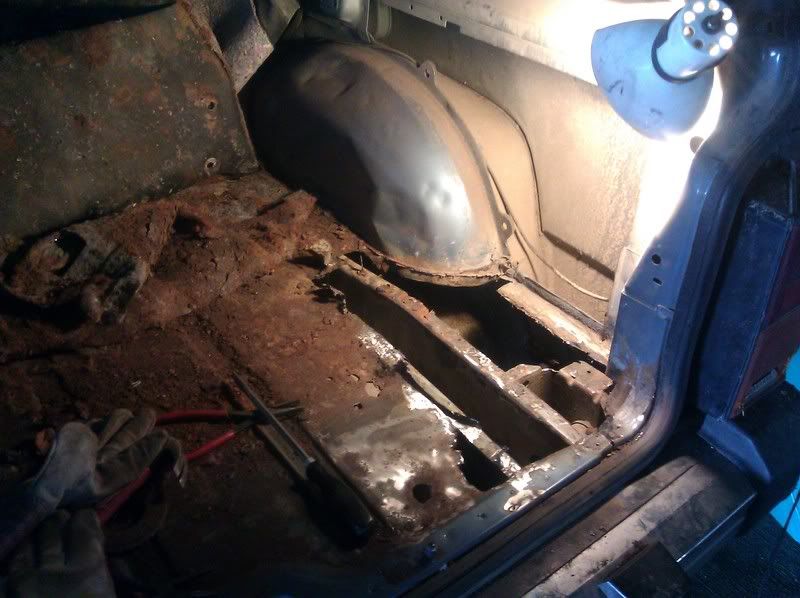
First couple pieces went pretty slow. Now that the corner is almost done I should be able to make fast progress.

#3
Thread Starter
Senior Member
Joined: Oct 2010
Posts: 562
Likes: 0
From: Pagosa Springs, Colorado
Year: 88-ish
Model: Cherokee
Engine: 4.0 I6

I had to pull the trim right where the rear hatch closes and then the side molding up to the back seats. But the carpet was also stuck to the floor from all the rust so it tore a little pulling up it too. Its getting trashed anyway so im not too worried about it.
#5
Thread Starter
Senior Member
Joined: Oct 2010
Posts: 562
Likes: 0
From: Pagosa Springs, Colorado
Year: 88-ish
Model: Cherokee
Engine: 4.0 I6

Going to start on a cage in the rear and then build storage around that. Then I'll lay down some bed liner so I don't get rust again. Bumpers after that and then we'll see what happens. The floor is going to take a while since I have full time work and a family too so I cant live in the garage. Plus the jeep still needs to see the mountains as often as possible while the weather is right.
#6
Thread Starter
Senior Member
Joined: Oct 2010
Posts: 562
Likes: 0
From: Pagosa Springs, Colorado
Year: 88-ish
Model: Cherokee
Engine: 4.0 I6

Made a little more progress yesterday but I ran out of metal so I have to hit up the sheet metal shop today to get some more scrap. Ugly welds but its solid.



Trending Topics
#9
Thread Starter
Senior Member
Joined: Oct 2010
Posts: 562
Likes: 0
From: Pagosa Springs, Colorado
Year: 88-ish
Model: Cherokee
Engine: 4.0 I6

Just a cheapo 90amp harbor freight one. The only thing different I did with it is put Lincoln wire in it instead of the crap it comes with. I know its crappy welder but its covered for two years even if I break and at this rate its going to pay itself off fast.
#10
Senior Member
Joined: Apr 2010
Posts: 720
Likes: 1
From: Marshall, WI
Year: 1994
Model: Cherokee
Engine: 4.0L i6

ugly welds??? screw that!!!! we all gotta start somewhere and why not with our own rigs!!! great job man!!! keep up the good work and before you know it you will be a welding expert!!! (or something close to it :P )
#11
Senior Member
Joined: Apr 2011
Posts: 620
Likes: 1
From: cedar rapids
Year: 99
Model: Cherokee
Engine: 4 ohh

Yeah its a good start. I think the hardest part of welding is getting it dialed in. Personally I would use at least a 120. But that's all I own at the moment. A nice 220 will do anything you want. Just try and get that 90 dialed in just right so you can keep a nice bead going. Make sure both surfaces are cleaned up and free of dirt grease or other details debris.

#12
Thread Starter
Senior Member
Joined: Oct 2010
Posts: 562
Likes: 0
From: Pagosa Springs, Colorado
Year: 88-ish
Model: Cherokee
Engine: 4.0 I6

Yeah its a good start. I think the hardest part of welding is getting it dialed in. Personally I would use at least a 120. But that's all I own at the moment. A nice 220 will do anything you want. Just try and get that 90 dialed in just right so you can keep a nice bead going. Make sure both surfaces are cleaned up and free of dirt grease or other details debris.


#14

yikes lol.. just my .02 but i work in a bodyshop and if you want to have any hope at all of saving that jeep id suggest cutting out the plates youve already installed. it really should have a solid piece cut out of that other sheet you have. with the placement of the welds right on top of the frame rails like they are now it wont hold up to stress. id suggest removing the plates, cutting back the rust as far as you can and replacing it with a solid sheet. try to cut it back to a factory seam if possible.. make solid welds where the sheet meets the floor and preform spot welds from the bottom where the frame rail meets the new sheet. and try to use some pretty thick sheet.. it really couldnt hurt. also try to strip down the other rail or even better grab a buddies non rusty jeep (if one actually exists LOL!) and try to copy the look and placement of the factory welds? and try to use seamsealer on all of the seams you weld on the floor and framerail and a good primer and paint otherwise its just going to rust away again. and also while welding back there its always a good idea to drop the gas tank.. youll get a much higher quality repair when youre not worried about blowing yourself up the whole time


#15
Thread Starter
Senior Member
Joined: Oct 2010
Posts: 562
Likes: 0
From: Pagosa Springs, Colorado
Year: 88-ish
Model: Cherokee
Engine: 4.0 I6

yikes lol.. just my .02 but i work in a bodyshop and if you want to have any hope at all of saving that jeep id suggest cutting out the plates youve already installed. it really should have a solid piece cut out of that other sheet you have. with the placement of the welds right on top of the frame rails like they are now it wont hold up to stress. id suggest removing the plates, cutting back the rust as far as you can and replacing it with a solid sheet. try to cut it back to a factory seam if possible.. make solid welds where the sheet meets the floor and preform spot welds from the bottom where the frame rail meets the new sheet. and try to use some pretty thick sheet.. it really couldnt hurt. also try to strip down the other rail or even better grab a buddies non rusty jeep (if one actually exists LOL!) and try to copy the look and placement of the factory welds? and try to use seamsealer on all of the seams you weld on the floor and framerail and a good primer and paint otherwise its just going to rust away again. and also while welding back there its always a good idea to drop the gas tank.. youll get a much higher quality repair when youre not worried about blowing yourself up the whole time


