Welding thread!!!!
#1711
Member
Join Date: Mar 2016
Location: Tempe, AZ
Posts: 113
Likes: 0
Received 0 Likes
on
0 Posts
Year: 1989
Model: Comanche
Engine: 4.7 stroker

time to bring the flame! haha
im a pretty novice welder. i couldnt guess at how many hours i put under a hood, but ive built a few small carts, shelves, fire pits, odds and ends, and ive been working on a custom radio flyer for my daughter. in my opinion i can weld thicker material "decently" (not very pretty) but still struggle with the thin stuff.
i just pulled my HP D60 out and plan to cut all the current bracketry off and weld on some stuff from ballistic and ruff stuff in order to stretch the front out a few inches, and possibly build a 3 link while im at it.
i just thought id ask for some ways i could improve my welds tips/pointers/criticism before hand. my setup is a millermatic 180 with 75/25 .030 wire


heres a few pics of things ive boogered together. most are for my daughters wagon, and a piece for my brothers roll cage. alot of the wagon welds were done at work usuing a 480V millermatic 250
wagon parts



this ones embarrassing...



how her wagon sits now

roll cage piece for my brother. in my defense, the wind started RIPPING when i was welding this





flame on! haha
im a pretty novice welder. i couldnt guess at how many hours i put under a hood, but ive built a few small carts, shelves, fire pits, odds and ends, and ive been working on a custom radio flyer for my daughter. in my opinion i can weld thicker material "decently" (not very pretty) but still struggle with the thin stuff.
i just pulled my HP D60 out and plan to cut all the current bracketry off and weld on some stuff from ballistic and ruff stuff in order to stretch the front out a few inches, and possibly build a 3 link while im at it.
i just thought id ask for some ways i could improve my welds tips/pointers/criticism before hand. my setup is a millermatic 180 with 75/25 .030 wire


heres a few pics of things ive boogered together. most are for my daughters wagon, and a piece for my brothers roll cage. alot of the wagon welds were done at work usuing a 480V millermatic 250
wagon parts



this ones embarrassing...



how her wagon sits now

roll cage piece for my brother. in my defense, the wind started RIPPING when i was welding this





flame on! haha
#1712

Originally Posted by wheelsaz08
time to bring the flame! haha
im a pretty novice welder. i couldnt guess at how many hours i put under a hood, but ive built a few small carts, shelves, fire pits, odds and ends, and ive been working on a custom radio flyer for my daughter. in my opinion i can weld thicker material "decently" (not very pretty) but still struggle with the thin stuff.
i just pulled my HP D60 out and plan to cut all the current bracketry off and weld on some stuff from ballistic and ruff stuff in order to stretch the front out a few inches, and possibly build a 3 link while im at it.
i just thought id ask for some ways i could improve my welds tips/pointers/criticism before hand. my setup is a millermatic 180 with 75/25 .030 wire


heres a few pics of things ive boogered together. most are for my daughters wagon, and a piece for my brothers roll cage. alot of the wagon welds were done at work usuing a 480V millermatic 250
wagon parts



this ones embarrassing...



how her wagon sits now

roll cage piece for my brother. in my defense, the wind started RIPPING when i was welding this





flame on! haha
im a pretty novice welder. i couldnt guess at how many hours i put under a hood, but ive built a few small carts, shelves, fire pits, odds and ends, and ive been working on a custom radio flyer for my daughter. in my opinion i can weld thicker material "decently" (not very pretty) but still struggle with the thin stuff.
i just pulled my HP D60 out and plan to cut all the current bracketry off and weld on some stuff from ballistic and ruff stuff in order to stretch the front out a few inches, and possibly build a 3 link while im at it.
i just thought id ask for some ways i could improve my welds tips/pointers/criticism before hand. my setup is a millermatic 180 with 75/25 .030 wire


heres a few pics of things ive boogered together. most are for my daughters wagon, and a piece for my brothers roll cage. alot of the wagon welds were done at work usuing a 480V millermatic 250
wagon parts



this ones embarrassing...



how her wagon sits now

roll cage piece for my brother. in my defense, the wind started RIPPING when i was welding this





flame on! haha
#1713
Seasoned Member
Join Date: Mar 2015
Location: Portland, OR
Posts: 280
Likes: 0
Received 0 Likes
on
0 Posts
Year: 1998
Model: Cherokee
Engine: 4.0L

Looks like a little extra prep here could be needed. I can't tell, but it looks like a little undercut.

#1714
Banned
Join Date: Feb 2014
Location: Florida
Posts: 2,379
Likes: 0
Received 17 Likes
on
16 Posts
Year: 2000
Model: Cherokee(XJ)
Engine: Golen 4.6L

And both of these classes have been a sort of "work at your own pace" type of thing where you can come back as many times as you're willing to pay for and build on what you already know. Last term one of the students was actually a welding inspector there to collect hours under the hood for recertification.
Now I think it's time for me to practice and build some things on my own for a while, but I could easily see myself going back at some point in the future, maybe under yet another instructor to get more variety.
#1715
Member
Join Date: Feb 2014
Location: Virginia
Posts: 168
Likes: 0
Received 0 Likes
on
0 Posts
Year: 1999
Model: Cherokee
Engine: 4.0

This has probably been asked before, but I can't find a decent answer anywhere. Hopefully someone can help me out.
I'm completely new to MIG welding. Bought a hobart handler 140 a few weeks ago and after sorting out a couple of issues it's doing well... on flux core. It's messy, but it holds.
I'd like to get a gas setup, but the nearest welding store is about an hour away from me and there aren't multiple around here.
I'm pretty sure I'm looking for 75/25 Argon/CO2 for my needs (Jeep and other small projects), but how much of that do I need? I don't have a lot of large projects ahead of me, but I practice regularly making things out of horseshoes, scrap, etc.
And what would be a fair price for that and a bottle?
Also does 75/25 work at all for stainless? I need to do an exhaust on my truck, which has factory stainless. It doesn't need to look pretty, so I can buy the stainless steel flux core if it wouldn't work at all.
I'm completely new to MIG welding. Bought a hobart handler 140 a few weeks ago and after sorting out a couple of issues it's doing well... on flux core. It's messy, but it holds.
I'd like to get a gas setup, but the nearest welding store is about an hour away from me and there aren't multiple around here.
I'm pretty sure I'm looking for 75/25 Argon/CO2 for my needs (Jeep and other small projects), but how much of that do I need? I don't have a lot of large projects ahead of me, but I practice regularly making things out of horseshoes, scrap, etc.
And what would be a fair price for that and a bottle?
Also does 75/25 work at all for stainless? I need to do an exhaust on my truck, which has factory stainless. It doesn't need to look pretty, so I can buy the stainless steel flux core if it wouldn't work at all.
#1716

Originally Posted by indeepwithajeep
Personally I think he's doing great for just starting out. Maybe a little bit of extra prep might get him some better penetration. The problem with that technique is that you're not keeping the heat in the root of the joint. I avoid that at all costs unless you're really needing to fill a gap you can't close otherwise.
Looks like a little extra prep here could be needed. I can't tell, but it looks like a little undercut.

Looks like a little extra prep here could be needed. I can't tell, but it looks like a little undercut.

#1717
Seasoned Member
Join Date: Mar 2015
Location: Portland, OR
Posts: 280
Likes: 0
Received 0 Likes
on
0 Posts
Year: 1998
Model: Cherokee
Engine: 4.0L

This has probably been asked before, but I can't find a decent answer anywhere. Hopefully someone can help me out.
I'm completely new to MIG welding. Bought a hobart handler 140 a few weeks ago and after sorting out a couple of issues it's doing well... on flux core. It's messy, but it holds.
I'd like to get a gas setup, but the nearest welding store is about an hour away from me and there aren't multiple around here.
I'm pretty sure I'm looking for 75/25 Argon/CO2 for my needs (Jeep and other small projects), but how much of that do I need? I don't have a lot of large projects ahead of me, but I practice regularly making things out of horseshoes, scrap, etc.
And what would be a fair price for that and a bottle?
Also does 75/25 work at all for stainless? I need to do an exhaust on my truck, which has factory stainless. It doesn't need to look pretty, so I can buy the stainless steel flux core if it wouldn't work at all.
I'm completely new to MIG welding. Bought a hobart handler 140 a few weeks ago and after sorting out a couple of issues it's doing well... on flux core. It's messy, but it holds.
I'd like to get a gas setup, but the nearest welding store is about an hour away from me and there aren't multiple around here.
I'm pretty sure I'm looking for 75/25 Argon/CO2 for my needs (Jeep and other small projects), but how much of that do I need? I don't have a lot of large projects ahead of me, but I practice regularly making things out of horseshoes, scrap, etc.
And what would be a fair price for that and a bottle?
Also does 75/25 work at all for stainless? I need to do an exhaust on my truck, which has factory stainless. It doesn't need to look pretty, so I can buy the stainless steel flux core if it wouldn't work at all.
#1718
Member
Join Date: Oct 2015
Location: Portland, OR
Posts: 109
Likes: 0
Received 0 Likes
on
0 Posts
Year: 1986
Model: Cherokee
Engine: 2.8

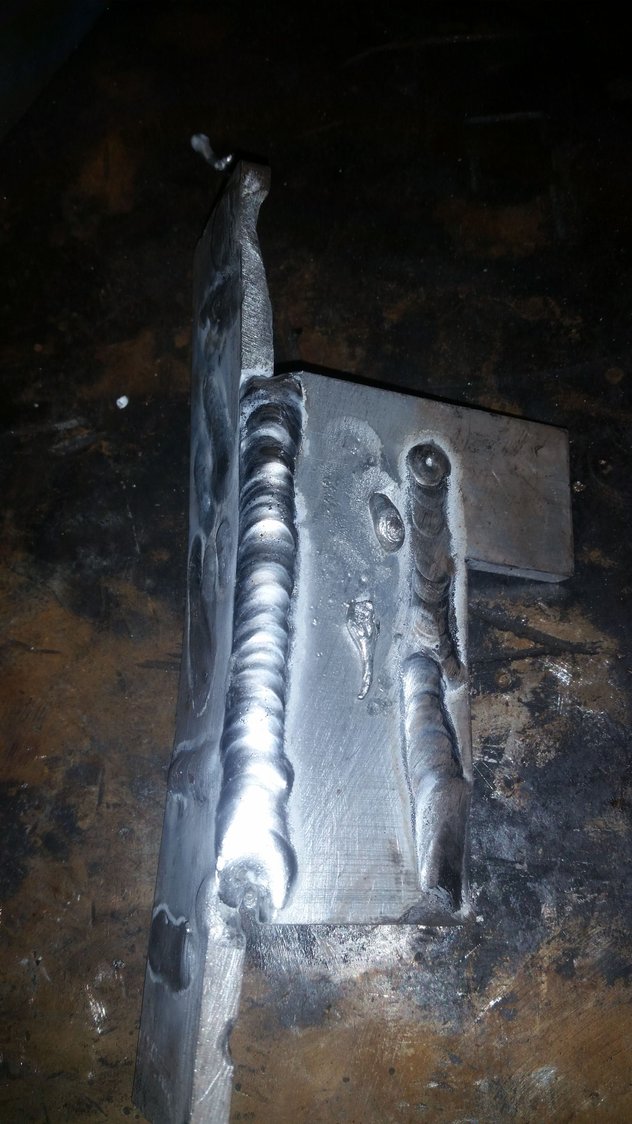
this is my first attempt at TIG with aluminum. did zero prep work and was mainly just killing time at work relearning TIG. my steel tig isnt too horrible but needs some work
#1721
Member
Join Date: Oct 2015
Location: Portland, OR
Posts: 109
Likes: 0
Received 0 Likes
on
0 Posts
Year: 1986
Model: Cherokee
Engine: 2.8

thanks, I need to start logging more time on aluminum. it also doesnt help I am stuck with one set of tungstens and not much scrap
#1723
No, I don't lick fish.

Exhaust adapter that got TIG welded today.
(Made about 50 today)
Welded using 309 stainless steel filler with two passes at 125 amps DC.
Attachment 287194
(Made about 50 today)
Welded using 309 stainless steel filler with two passes at 125 amps DC.
Attachment 287194
Speaking of awesome welds (queue sarcasm).... can anyone give me a solid recommendation for flux-core wire? Not looking for diameter, 'cause my machine will only handle up to .035" anyway... need to know what brand. I've had a couple of people say INE, but then I look and supposedly INE is now made by the same company that makes the Harbor Freight wire. I'd like to try a better quality wire 'cause I've heard from many that a quality wire can make a difference in this stupid little HF buzz box.
Mainly asking 'cause I'm out of wire.
#1724
CF Veteran
Join Date: Jan 2013
Location: west chester, pa
Posts: 19,216
Likes: 0
Received 40 Likes
on
36 Posts
Year: 1999
Engine: 4.0

Gorgeous! Speaking of awesome welds (queue sarcasm).... can anyone give me a solid recommendation for flux-core wire? Not looking for diameter, 'cause my machine will only handle up to .035" anyway... need to know what brand. I've had a couple of people say INE, but then I look and supposedly INE is now made by the same company that makes the Harbor Freight wire. I'd like to try a better quality wire 'cause I've heard from many that a quality wire can make a difference in this stupid little HF buzz box. Mainly asking 'cause I'm out of wire.
#1725
No, I don't lick fish.