RoofRack Without Welding?
#16
CF Veteran
Joined: Jul 2009
Posts: 1,640
Likes: 0
From: Keesler AFB, MS
Year: 1998 XJ
Model: Cherokee
Engine: 4.0L

Thanks fella's for the nice comments, This was the first thing i have ever actually built, I have sold a few since the first one (which is still on my jeep). Reason i said that is bc if i can build it, you can build it. I have not had any issues what so ever. It has taken a lot of abuse off road and still no squeking or breaking at all. Can't remember if i put the instructions and what exactly you will need in the old thread so i will post ot again. Good luck and like the guy said before, measure twice and cut once. If you have any further questions. let me know. Also if for somereason you need it stronger (like the floor). Swap in some rigid conduit.
you will need
four 10' pieces of 1" emt conduit (Rails)
three 10' pieces of 1/2" emt conduit (floor)
about 8' of 1/4" x 1" aluminum strip (supports)
2 boxes of self tapping screws
3' of 3/4" galvanized steel pipe (for bushings) from plumbing section
1" Tube bender (rent)
four 1" u bolts (to mount)
2 pieces of thin 12" x 24" diamond plate (optional)
buy a big big square (10 bucks at lowes)
i used the square to make a jig out of 2x4 wood. that was my template to make sure all of my bends were the same.
if you use your factory roof rack to mount it on your width will be 42". my length is 58" but this depends on what you want.
take 1 piece of conduit, make your measurements (mine was 58" front to back) this will probably sound confusing but i will try to explain anyway. your piece of conduit is 120" long. minus 120" by 58" and that leaves you with 62. half of 62" is 31". now you should measure in 31" from one end of the conduit and mark it, now do the same from the other end. you should have 58" in between both your marks. there is a star on the bender. use that as your marker every time and bend 2 90 degree bends into it so it looks like this [. Take the other 3 pieces and bend them the exact same way. you can cut off the excess later to make it 42" wide. make sure all your pieces are exactly the same. now overlap them like this [] and using a square. Measure 10 times cut once. cut off the same amount on each end to make it 42" wide when the ends are butted together.
you will have to grind some of the outer diameter of the 3/4" galvanized steel pipe for it to fit inside the 1" emt. then after it will fit inside the emt, cut four 6" pieces. this will be used to connect both sides of the emt conduit. put 3" in one side and secure and then the other 3" inside the other side.
now use your bushings to connect each side top and bottom and make sure they are the exact same. great thing about self tapping screws is that you can removed them and fix your mistakes unlike welding.
With the aluminum strip. cut it into 5" pieces. Or however tall you want it. it should make around 18 or 19. make sure they are all the same length. you will need to predrill these holes. i used a gig on this also to make sure all my holes in each end would look the same. i will try to upload more pics of these items and jigs tonight. evenly space however many supports you want on each side. i started in the middle of each side then 1/2'd each remaining distance and put another support. when the top and bottom are connected now is a good time to grind down any flaws or sharp points you want to. i ground down flush the ends of my supports. you will need to do this atleast on the bottom to install your floor later.
now once all that is done you can install the floor. measure from one side to the other. you can see on the pics in my profile that i connnected my flooring right under my supports. once you have cut all your 1/2" conduit pieces to the same length. you will need to flatten each end so they will connect flush on the bottom of the rack. predrill these holes and then install. grind down the rough edges. if you want to put thin pieces of diamond plate sheet metal on the corners, now is the time. this is up to you and you can make it look the way you want it. i hope i have explained everything and it is understandable. good luck and send me some pics when your dine. there was a lot of measuring and squaring up. this was the first thing i have ever made and fab'd up. i only made one mistake, i said that just to say this. if you take your time and make sure your measurments are good. it is easy.
hopefully i didn' leave anything out
Pics are in my albums under roof rack. and i also since then have built a light bar for it out of 1" angle iron and 4 emt conduit wall hangars. I can take and post some close up pics if anyone needs them.
let me know how it works out for you.
later
rusty
you will need
four 10' pieces of 1" emt conduit (Rails)
three 10' pieces of 1/2" emt conduit (floor)
about 8' of 1/4" x 1" aluminum strip (supports)
2 boxes of self tapping screws
3' of 3/4" galvanized steel pipe (for bushings) from plumbing section
1" Tube bender (rent)
four 1" u bolts (to mount)
2 pieces of thin 12" x 24" diamond plate (optional)
buy a big big square (10 bucks at lowes)
i used the square to make a jig out of 2x4 wood. that was my template to make sure all of my bends were the same.
if you use your factory roof rack to mount it on your width will be 42". my length is 58" but this depends on what you want.
take 1 piece of conduit, make your measurements (mine was 58" front to back) this will probably sound confusing but i will try to explain anyway. your piece of conduit is 120" long. minus 120" by 58" and that leaves you with 62. half of 62" is 31". now you should measure in 31" from one end of the conduit and mark it, now do the same from the other end. you should have 58" in between both your marks. there is a star on the bender. use that as your marker every time and bend 2 90 degree bends into it so it looks like this [. Take the other 3 pieces and bend them the exact same way. you can cut off the excess later to make it 42" wide. make sure all your pieces are exactly the same. now overlap them like this [] and using a square. Measure 10 times cut once. cut off the same amount on each end to make it 42" wide when the ends are butted together.
you will have to grind some of the outer diameter of the 3/4" galvanized steel pipe for it to fit inside the 1" emt. then after it will fit inside the emt, cut four 6" pieces. this will be used to connect both sides of the emt conduit. put 3" in one side and secure and then the other 3" inside the other side.
now use your bushings to connect each side top and bottom and make sure they are the exact same. great thing about self tapping screws is that you can removed them and fix your mistakes unlike welding.
With the aluminum strip. cut it into 5" pieces. Or however tall you want it. it should make around 18 or 19. make sure they are all the same length. you will need to predrill these holes. i used a gig on this also to make sure all my holes in each end would look the same. i will try to upload more pics of these items and jigs tonight. evenly space however many supports you want on each side. i started in the middle of each side then 1/2'd each remaining distance and put another support. when the top and bottom are connected now is a good time to grind down any flaws or sharp points you want to. i ground down flush the ends of my supports. you will need to do this atleast on the bottom to install your floor later.
now once all that is done you can install the floor. measure from one side to the other. you can see on the pics in my profile that i connnected my flooring right under my supports. once you have cut all your 1/2" conduit pieces to the same length. you will need to flatten each end so they will connect flush on the bottom of the rack. predrill these holes and then install. grind down the rough edges. if you want to put thin pieces of diamond plate sheet metal on the corners, now is the time. this is up to you and you can make it look the way you want it. i hope i have explained everything and it is understandable. good luck and send me some pics when your dine. there was a lot of measuring and squaring up. this was the first thing i have ever made and fab'd up. i only made one mistake, i said that just to say this. if you take your time and make sure your measurments are good. it is easy.
hopefully i didn' leave anything out
Pics are in my albums under roof rack. and i also since then have built a light bar for it out of 1" angle iron and 4 emt conduit wall hangars. I can take and post some close up pics if anyone needs them.
let me know how it works out for you.
later
rusty
#17

I am in the process of building one with EMT. I have my main hoops finished and im going to work on a floor and then struts. I made my bends in 4 pieces just 90's cut to legenth and connected them with steel EMT couplers.
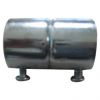
Once the floor and the supports are in I will remove the screws and pop rivet them so theres less chance of something working loose. Im still debating on what to construct the base with, most likely some 1/2" square tubing or just more 1/2" EMT. Ill post pictures up later.
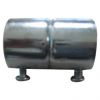
Once the floor and the supports are in I will remove the screws and pop rivet them so theres less chance of something working loose. Im still debating on what to construct the base with, most likely some 1/2" square tubing or just more 1/2" EMT. Ill post pictures up later.
#21
CF Veteran
Joined: Nov 2009
Posts: 2,372
Likes: 0
From: perrysburg
Year: 1995
Model: Cherokee
Engine: 4.0L 6cyl
#22
CF Veteran
Joined: Jul 2009
Posts: 1,640
Likes: 0
From: Keesler AFB, MS
Year: 1998 XJ
Model: Cherokee
Engine: 4.0L
#23
Seasoned Member
Joined: Jan 2009
Posts: 375
Likes: 1
From: Lovettsville, VA
Year: 1996
Model: Cherokee
Engine: 4.0

Warthog,
How did you wire up the lights? Where did your route the wires? Also, if you were to do it over, what would you do different? By the way, it looks great! It gives me a goal for what I want mine to look like.
How did you wire up the lights? Where did your route the wires? Also, if you were to do it over, what would you do different? By the way, it looks great! It gives me a goal for what I want mine to look like.
#24
CF Veteran
Joined: Jul 2009
Posts: 1,640
Likes: 0
From: Keesler AFB, MS
Year: 1998 XJ
Model: Cherokee
Engine: 4.0L

Thanks,
I ran the wires down the left side and into the rail that runs along the left side of the jeep towards the back. Then inside thru the back hatch. I check the wires periodically for signs of chafing. I have had the wires running thru the back hatch for 6 months now and they still look brand new. But for safety reasons, make sure you keep inspecting them for wear. From the back hatch i ran them under all the trim and back to the front. I have a lot of pics of where i ran the wires in this link. https://www.cherokeeforum.com/member...8/albums/post/
Now for what i would have done differently. I would have paid more attention to the way pre made shovel and hi lift mounts are designed so i could have built an easy way to attach them to the rack, I know am right in the middle of fabbing up some claps/brakets for those items. I would have also bought two more stock cross rails to mount the rack on, making four total. That would have givin it more support. My current setup i know will hold 200lbs plus. but if i put 2 more cross rails on it to mount the rack to, it might hold over 400lbs, not that i will ever need it to hold that much but you never know. The last thing is i would have used 1/2" rigid conduit instead of emt for the floor because they are atleast twice as strong.
Great questions
Rusty
Last edited by warthog; 02-22-2010 at 06:19 PM.
#25
CF Veteran
Joined: Nov 2009
Posts: 2,372
Likes: 0
From: perrysburg
Year: 1995
Model: Cherokee
Engine: 4.0L 6cyl
#26
CF Veteran
Joined: Jul 2009
Posts: 1,640
Likes: 0
From: Keesler AFB, MS
Year: 1998 XJ
Model: Cherokee
Engine: 4.0L
#27

How are your floor braces attached? Just flattened the ends and screwd them into the frame? I was looking at using rigid or possibly 1/2" square turbing on my floor .
#29
#30
CF Veteran
Joined: Jul 2009
Posts: 1,640
Likes: 0
From: Keesler AFB, MS
Year: 1998 XJ
Model: Cherokee
Engine: 4.0L